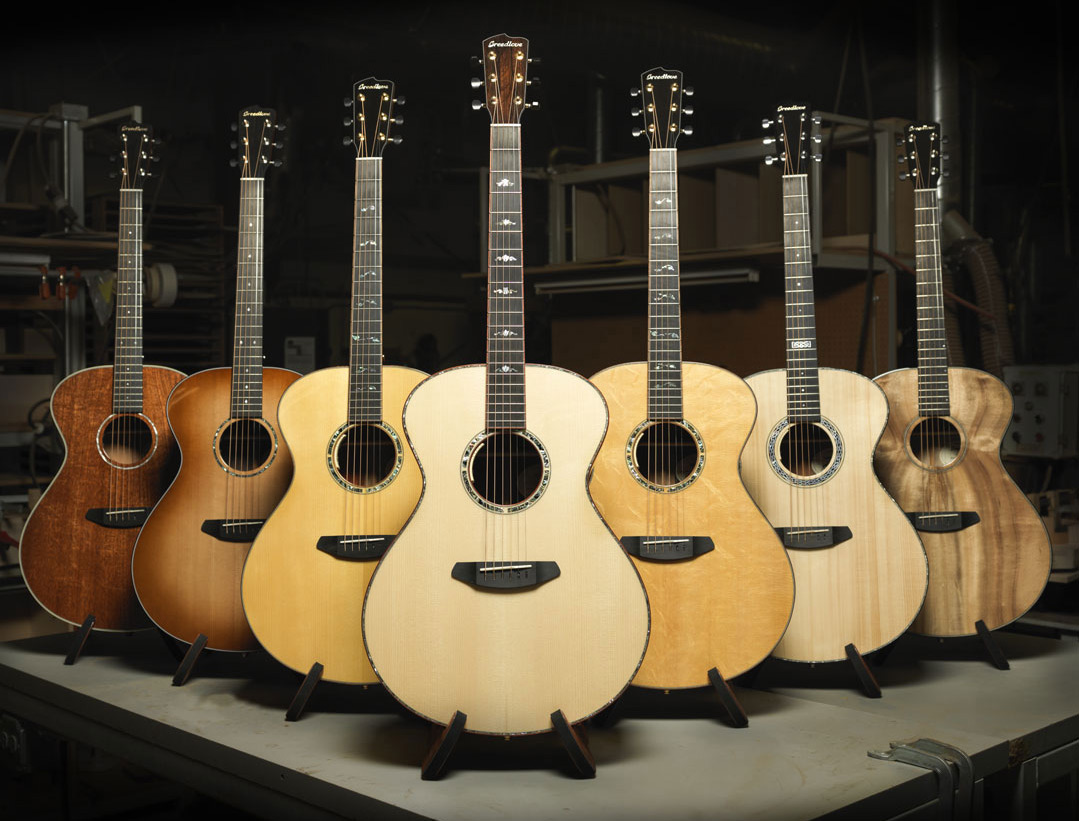
Born in a Barn
In 1990, pioneering California luthiers Larry Breedlove and Steve Henderson did something crazy. They left stable jobs at Taylor Guitars in sunny San Diego County to start their own business in the mountains of the Pacific Northwest. The duo landed in tiny Tumalo, Oregon, just northwest of Bend, opening shop in an old barn.
But this was no simple mountain aerie. They were not trying to immerse themselves in a pastoral landscape to practice archaic guitar art. They wanted a laboratory, a place with the freedom to test out their wildest concepts. Breedlove and Henderson built better guitars through experimentation—challenging assumptions about lutherie with completely original concepts like graduated tops, unique tonewoods, bridge trusses, asymmetrical headstocks, and winged bridges. Not all of those experiments survived the test of time. Breedlove no longer builds guitars with graduated tops, and the bridge truss is only used in a handful of specific models. Those early creative efforts, however, yielded groundbreaking fingerstyle instruments and established Breedlove as a guitar manufacturer grounded in tradition but looking toward the future.
In 1994, two years after the company officially launched their new designs, Larry’s brother Kim joined as master luthier. Kim eventually steered the brand through nearly 25 years of sonic metamorphosis, facilitating breakthrough after breakthrough. Breedlove refined traditional assembly methods and invented radical new body shapes.
Bought by a Hippy
Two Old Hippies Guitars, led by Tom Bedell, purchased Breedlove in November 2010. Stories of innovative, boutique brands getting gobbled up by corporate ownership, stripped of their souls, and perverted for profit feel all too familiar in the 21st Century. But that was never Bedell’s intention, and that’s not what he’s done. The past dozen years have seen Breedlove maintain its roots in central Oregon. The company continues to innovate in sound design while also realizing new visions for the brand that have nothing to do with profit.
“Breedlove has continued, really, from the dreams of Larry and Steve,” Bedell says. “Everything we’re doing today is still based on innovation and customization. Those are the themes that inspire us. We’re constantly learning. It’s just this real passion to create the best sounding instruments possible.”
Breedlove HR Manager Terri Hensley was there not long after the start, in the Tumalo days.
“Many of our craftspeople,” Hensley says, “have been here for years. They’ll stop us as we walk through the workshop just to show us a remarkable piece of wood, almost giddy, saying, ‘I can’t wait to see and hear this when it’s done.’ They’re just so excited, still, which I love, after so many years.”
Design meets science in Bend, just as it did at the beginning of Breedlove. As innovation demands, some of the founders’ concepts have been altered or left behind, with fresh ideas building on core principles.
“Every day,” says Bedell, “we’re continuing the tradition of looking forward that Breedlove started with back in 1990.”
Enhanced by Science and Technology
Breedlove is the only guitar manufacturer to utilize Sound Optimization. This meticulous and carefully monitored process ensures that raw wood sets realize their greatest potential as guitars. Builders combine the ancient art of tone tapping—tapping on raw wood and listening for particular properties, used by icons of the stringed instrument craft like Stradivari—with modern technology and proprietary software. Builders can account for the specific densities of discrete wood sets as well as top and back frequency separation. The result? Guitars that embrace and harness the unique characteristics of the living wood from which they were fashioned rather than constraining those woods to a preconceived design.
When chief product designer Angela Christensen (who apprenticed under Kim Breedlove) thinks about guitars, she is always thinking about Sound Optimization. She’s also thinking about the unique relationship between an instrument’s body shape and size and the dimension of the soundhole, and how those parameters will interact with different species of wood cut to carefully determined specifications.
Continuing to Innovate
“A big part of Breedlove’s history,” says Bedell, “has to do with redefining body shapes. We keep the very first Concert (which Bedell acquired from Larry Breedlove) ever made on display in the lobby!”
“Before we developed the Breedlove Concert, Concerto, and Concertina [Breedlove’s proprietary body shapes], you had to compromise between volume, projection, overtones, and complexity. We’ve worked really hard at giving you all of that in an instrument that feels natural and easy to play.”
In addition to optimizing the sound of individual instruments and inventing new acoustic guitar body shapes, Breedlove has also successfully integrated new tonewoods. They were the first acoustic guitar brand to realize the potential of myrtlewood, which produces an ideal sonic blend of rosewood, mahogany, and maple. Myrtlewood also makes sense for an Oregon-based business because it only grows in the Pacific Northwest.
“Myrtlewood has been a real breakthrough,” Bedell says. “Of all the tonewoods that exist on earth, myrtlewood is one of the top two or three in terms of the sound it creates.”
“When we were introducing it in the ’90s,” Hensley, an eager Breedlove historian, chuckles, “nobody knew what it was. It’s a great tonewood and other builders weren’t using it. Half of our USA Breedlove guitars now feature it.”
Understanding our Impact
Bedell didn’t drastically alter the identity of the company, but he did add his values. One of the primary changes that Bedell instituted when he took the helm was to focus on where the source materials came from and what impact they have on the environment.
“The owner before me had no idea where the wood came from,’ says Bedell. “It never occurred to him to think about, ‘Where did the tree grow? What impact might the harvest have had on the sustainability of our forests?”
Tom Bedell cares deeply about environmental stewardship and set a goal for the company to become leaders in the industry.
“We set a policy of using no clear cut trees in any of our guitars, of only individually harvesting trees, and doing everything we could to protect the forest community and neighborhood. And we made a policy that any mill we work with would protect the [local] wildlife, human habitat, and forest.”
Bedell’s goal is to push every guitar manufacturer in the hope that they too not only do less harm, but help protect and restore our world’s forests.
“I thought, if I could sent an example that others would follow, I could make a difference.”
Building Guitars for Everyone
In addition to sustainability, Bedell also set a goal of access and inclusivity. Breedlove started out as a boutique manufacturer, individually building custom guitars by hand. While that produces exceptional instruments, it also limits the number of people who can enjoy them. Over the past few years, Breedlove has released several new lines of guitars, like the Organic and ECO collections, that are accessible to players who can’t afford custom shop price tags. While not produced in the Bend, Oregon workshop, these instruments’ design DNA can be traced back to those heady days in a dilapidated barn. Not only do they benefit from the pioneering sound research that has been part of Breedlove Guitars from the beginning, they also maintain the modern Breedlove demand to use only sustainably sourced materials.
STILL Building Guitars in Bend
Though Breedlove has expanded its offerings to include players whose bank accounts can’t cover triple digit instruments, the brand and headquarters have never left central Oregon. The workshop is still right there in Bend, where a growing team of builders, designers, sound engineers, and luthiers are still making guitars and innovating new ways to make them sound even better. Unlike many of the major American guitar makers, instruments crafted at the Breedlove USA workshop are still made largely by hand, with nearly three dozen craftspeople, many players themselves, imprinting every guitar they touch.
“We’re able to build 2,000 guitars a year here in Bend,” Bedell says. “Every one is uniquely dimensioned to whatever the characteristic of that wood is and whatever we want that instrument to play like and sound like. We couldn’t do that if we didn’t hand build every guitar. It would be impossible.”