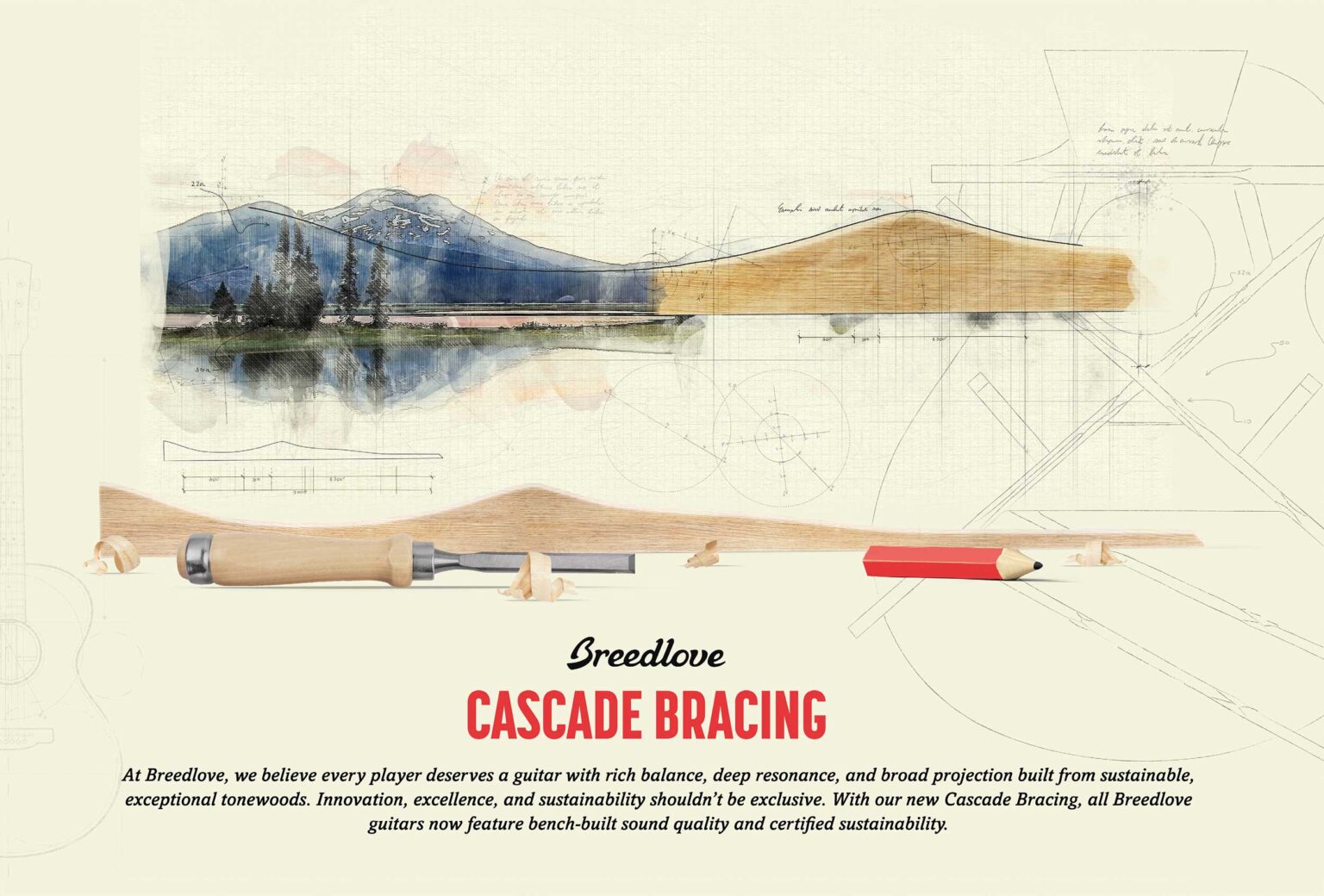
A couple of weeks ago, we explored the question, “what is bracing on an acoustic guitar?” The article overviews acoustic guitar bracing and briefly touches on our design called Cascade Bracing. Here, we want to get into Cascade Bracing a bit deeper, discussing what it is, how we created it, and why.
Acoustic Guitar Bracing Recap
Acoustic guitar bracing is the internal scaffolding that holds your guitar together. The thin strips of wood are attached to the soundboard’s underside and the guitar’s back. The design of these braces is also a crucial element in voicing the instrument. Though countless bracing patterns have come, gone, and still exist today, most modern steel-string acoustic guitars rely on X-bracing.
Cascade Bracing
X-bracing is so prevalent that most modern, alternative bracing patterns are adaptations of the design. That’s certainly true of our Cascade Bracing. But it’s in those adaptations that Cascade Bracing sets itself, and our Designed in Bend series acoustics, apart.
The difference quickly becomes evident if you look at the braces themselves. Unlike most other braces’ arrow-straight lines, they feature a series of peaks and valleys. These peaks remind us of the beautiful Cascade Mountains that dominate our hometown of Bend, Oregon, hence the name. But their contours are much more than a geological homage.
From Sound Optimization
Cascade bracing is born from the years of data we’ve pulled from our US factory’s proprietary hand-tuning process we call Sound Optimization. Breedlove Wood Management & Product Development Manager Angela Christensen explains Sound Optimization like this, “Starting with our raw wood sets, we treat every set of tonewood as a unique part. We individually serialize the wood sets so we can collect specific data; from sound frequency readings on the raw wood, and the instrument as it is being built, to the weight of the bridge, we collect over 40 data points on every guitar we make in our Bend factory. And we hand-tune every one of them to targeted frequencies.”
Over seven years of experience hand-tuning these guitars gave us detailed insight into how to make our Made in Bend guitars come alive. With that information in mind, we also wanted to apply it to our Designed in Bend series acoustics. While not individually hand-tuned, Cascade Bracing ensures these guitars offer the maximum response and tonal detail of guitars costing much more.
Tuned for Each Body Style
When guitarists play one of our Concerto guitars, they expect a bigger, warmer tone than from a smaller-bodied guitar. They also expect a balanced, nuanced sound from our Concert guitars. Because of this, we approached Cascade Bracing differently for each body style that features the pattern. This gives each guitar more of its natural voice and is a critical step in ensuring it is the best it can be.
But wait. There’s more.
Wood Thickness
Cascade Bracing goes way beyond the internal braces and tone bars themselves. The data gathered through Sound Optimization also informs our treatment of the guitars’ top, back, and sides. We can specify finely tuned thicknesses for all woods by species and uses. The magic in these guitars lies in the marriage of all of these construction techniques. Or, as Angela puts it, “All these things combined, and you have the new Cascade Bracing System.”
In Conclusion
An acoustic guitar’s bracing pattern is essential to its design and construction. Not only is it responsible for the instrument’s structural integrity, but it defines the guitar’s tone. X-bracing is the go-to pattern for steel-string acoustics worldwide, and for great reason. But our Cascade Bracing improves upon it by utilizing years of our Sound Optimization data. It gives your Designed in Bend Breedlove a carefully curated voice with the most detail, power, and response possible.
Try a Designed in Bend Breedlove for yourself and experience how carefully subtracting a bit of wood can add an astounding amount of tone.