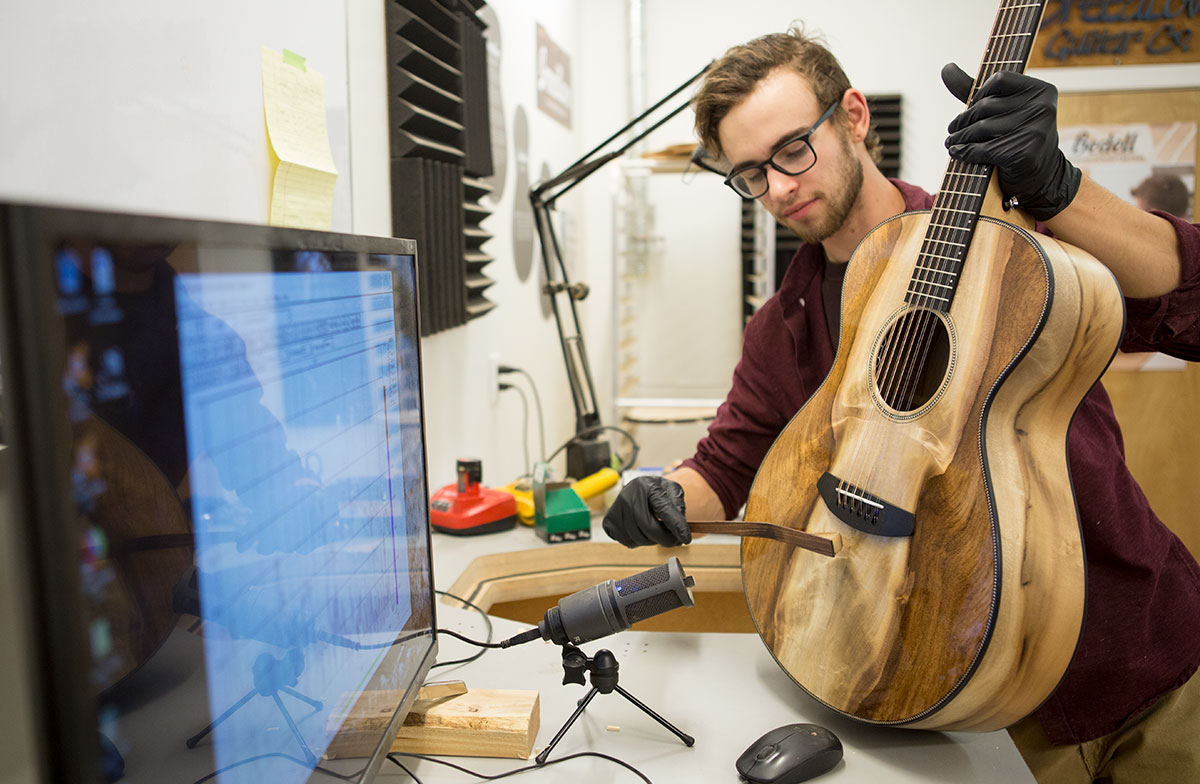
Sound Optimization. It’s the Breedlove Difference.
It’s what sets Breedlove apart.
It’s simple, really, applying science to every piece of wood at every step along the way, from tree to guitar.
If you’re a gear geek, you’ve probably heard of tap tones and that’s as good a place to start as any when considering Sound Optimization.
One of the standard memes of luthiery is the earnest builder, his ear to a newly sanded top, gently thumping the wood, dreamily sorting in his mind the frequencies emanating from the silky raw spruce or pungent mahogany.
That is a real thing, no doubt, but at Breedlove the sonic fingerprint of that tap with a voicing mallet goes straight into a microphone, with Fast Fourier Transform software creating a virtual snapshot of that individual piece of wood.
“In general terms,” says Breedlove Production Manager Miles Benefield, “Sound Optimization is the way we respect and respond to the variability of wood, so that we use each piece to its best potential. The way that's done is by analyzing each tonewood set and getting the Hertz readings for its individual length and width, which is how quickly sound is moving back and forth each way in the wood.”
But the story begins well before Benefield stands in front of that mic in Bend. It starts in the forest and it ends in your hands. Even in the field, before it’s milled and stored, only wood from fallen or selectively harvested trees is chosen. No clear-cut timber is used in domestic Breedloves. Sound Optimization is about building instruments the right way—the ethos of science and values harmoniously blended into each handcrafted guitar.
On Thursdays, when it’s time for Benefield to pull materials for the week’s production run, he keeps Sound Optimization in mind as well. It’s important to remember that Breedlove USA models are made with many of the traditional methods of handcrafting used in ancient Cremona violins, but the science lets the materials be at their best before they’re assembled.
“The process,” says Ian Schellinkhout, “allows the sound itself to not be impeded by the construction of the instrument.”
Wood taken from a single tree can vary as much as 30 percent in its density and frequency. Breedlove looks at all of these measurements, as well as the specific gravity of each species.
“Cocobolo, say, has a specific gravity of 1.1,” Benefield notes. “Whereas mahogany, at .59, is almost half that. In the past, we would have sanded both of those to the same thickness. Now, we'll sand each one to weight based on body shape. It really comes down to the mass of each piece and how it’s going to work with another.”
“Most of what people hear when they're listening to an acoustic instrument is the fundamental resonance,” Schellinkhout, who maintains sound quality assurance at Breedlove, says. “It's similar to the Helmholtz resonance you get when blowing across the top of an empty bottle. That plays into 90 percent of the actual tonal characteristic of an instrument. Sound Optimization allows us to hit certain consistent frequency separations with the top and the back, so they work together constructively.”
Careful pairing and matching, giving consideration to deflection, mass and body shape, targets the characteristic timbre of each model—with the ratio between top and back notes being greater, for example, in a large Concerto than a smaller Concertina.
In implementing Sound Optimization, which takes into account every element from wood species to body size and a player’s preferred attack, Breedlove, which pioneered the technology in a production setting, realized that the absolute best—and most consistent and reliable—sound would be realized by treating every aspect of a build uniquely.
Unlike most factory operations, it adds work; all with the goal of letting you sound better, play better and play more.
“It does multiply a lot of factors as far as the production process goes,” Schellinkhout says, “so now we have to work each piece individually instead of it being a batch process where 50 units are cut to the same thickness at the same time.”
For example, at the Hand Voicing Station, with an artist’s touch and a steampunk-looking fingerplane on his right hand, Schellinkhout shaves away a whisper from a tonebar glued to a gloriously-grained myrtlewood top. He’ll do the same—scraping a kiss this time—with a spruce brace on an East Indian rosewood back. He’s using the sense memory of his hands. He’s using his trained ear. But he’s also watching calculations from the FFT analyzer, knowing that the sets for every guitar made in Bend have to have that specific relationship to each other.
When all is said and done, Schellinkhout, more often than not, is the one who signs each Breedlove Guitar Portrait, which you’ll find in your case on delivery. That card is just what it says, featuring not only the model and serial number, but also its total weight, top and back thicknesses and frequencies, and the instrument’s own fundamental tone. The card is evidence of the science you strum, the music you make is the proof.
“It’s like a bellows,” Benefield says. “Whereas if the top and the back resonances are right on top of each other, the instrument’s just going to be really flat and not very responsive. They'll cancel each other out, which basically, in my opinion, is a dead guitar. With everything Sound Optimized, you just have that feeling you're connected to the instrument while you're playing it.”
If you are interested in learning more about the Breedlove Sound Optimization Process, we suggest downloading and reading The Breedlove Difference using the link below and another great article about the sound benefit achieved through the Sound Optimization Process.